For more than 20 years, a just in time philosophy has dominated supply chain thinking. With recent global events and the high probability of more to come, this almost certainly must change.
JIT. Kanban. Kaizen. Lean. Six Sigma. Words and concepts that have become synonymous with the manufacturing and supply chain sectors. Driven respectively out of Japan’s automotive excellence and General Electric’s ‘Lean’ waste elimination philosophies, they share the common goal of improving efficiency, reducing overheads, and extracting infinitely more value from production lines and supply chains.
These concepts have well served an increasingly global and diverse manufacturing base in an age where cost is king and inflation is low to steady. With the combination of increased wage pressure, particularly in construction, automotive, and heavy industry, this creates an evergreen pressure to do more with less.
My own first exposure to JIT et al came in the early 2000’s when I recruited in the labour hire sector in Melbourne. We worked extensively with Tier 2 and 3 automotive suppliers; some small-ish outfits supplying components to Toyota, Ford, and aftermarket resellers. We placed forkies and production workers, machinists and tradies. Even then they were in their death throes, beaten down by the year-on-year cost down pressures and mounting wage costs, although they refused to acknowledge the certainty of their demise.
But I remember driving to Laverton, Bayswater, or Dandenong, to see parts arriving just as needed to factories. They were just in time for production workers to add widgets to whatsits, returned in Kanban bins just in time to Avalon or Geelong or Footscray to be inserted into Falcons and Camrys. This was supply chain perfection.
Less need to store inventory means more ready cash flow, less need for warehousing, and the ability to switch on or off production as required.
Despite the death of automotive manufacturing in Australia this permeated all aspects of supply, from heavy industry to manufacturing to food and retail, from REPCO to Myer to BHP. And in a world where risk is low and supply chains are near constant, it works.
It might seem melodramatic to say, but we don’t live in that world anymore. I don’t need to list all the natural disasters we’ve experienced, and by the time you read this it may be out of date anyway. Add on COVID-19, Iranian tankers being blown up and threats to the global oil supply, and it feels like Billy Joel is overdue for a new verse to his famous anthem.
Put simply, we can no longer guarantee supply. COVID-19 is the perfect example of an event causing ripple effects across the global supply chain. Perhaps surprisingly, big pharma was the first to highlight these effects, not to mention the sudden and unquenchable desire for face masks and sanitiser in Asia. In Singapore and Hong Kong, stockpiling caused a brief but entertaining shortage of toilet paper (so that’s what a bidet is for!).
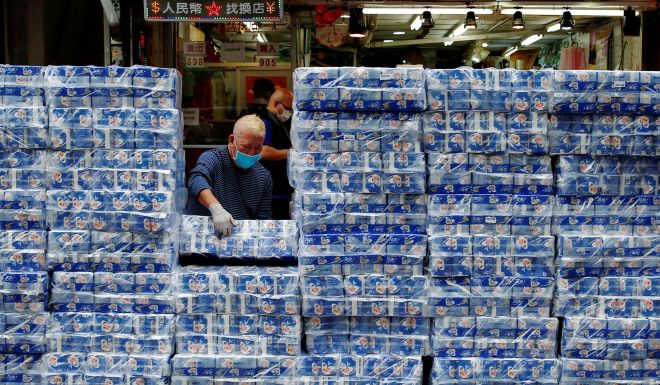
Food security seems flimsy at best when much of the lower eastern seaboard has been decimated by fire and flood. Burned paddocks means less grass, less milk, less beef, less lamb. Anecdotally, construction sites are running short of nails and other goods from China.
What does this mean and do I need to put a bomb shelter in my basement, I hear you ask? Well, no, but if you do, please extend me an open invite.
In all seriousness, what it means is that we need to rethink our approach to inventory and supply chain. Relying on JIT especially when it comes to wholly- or part-manufactured goods from China is now fraught with risk.
The good news is, there is already an exemplar of an alternative model to inventory risk in operation.
Our Defence Forces have long practiced pragmatic forms of inventory optimisation that can be applied to industry-based supply chain risk management.
The ADF would never be out of stock of even the slowest-moving items. They are well prepared for supply risks across diverse geographic regions and have built in contingencies should supply or suppliers fail. Often, these extra precautions are because they do rely on a single supplier for products (you can’t easy swap out an EF88 Austeyr rifle mag for an AK47 equivalent, surprisingly), but this should be equally relevant for industry as even when there are multiple suppliers they are often all based in the same geographic region. It’s not much use having multiple nail suppliers when all are affected by COVID-19.
So there’s no need to stock pile, but maybe there is a reason to stock up. And buy some extra loo paper, just in case.
* N.B. The author wrote this on Thursday 27th Feb and on date of posting the world has already changed – we’ve decided to leave the content untouched to show how quickly this situation is evolving.